目前广泛使用的直流发光二极体(DC),若要经由市电供电,须外加交流对直流(AC-DC)整流器,易造成额外物料成本及能源转换损失,因此产业界已发展出以交流电直接驱动的高压LED(HV LED),可大幅提升系统的能源利用率和发光效率。
在传统光源中,发光效率最好的是日光灯,其光源本身的发光效率约65lm/W。用于安定器的附加电路会造成13~20%的能源损耗,光源发光经过的反射罩,其光源效率损耗约30~40%,因此在实际的照明应用环境下,日光灯的灯具照明发光效率约35lm/W。虽然光源自身发光效率高,但附加电路和灯具结构所造成的光损失,将会大幅降低灯源的发光效率。
目前已大幅应用在照明光源的高功率白光直流发光二极体(DC LED)(表1),其光源发光效率可达150lm/W。但DC LED是以直流电源驱动操作,若要使用在市电上,势必要外加交流对直流(AC-DC)整流器,电源转换将会造成20~30%的能源损耗,且驱动电路之体积也较为庞大,灯具设计弹性相对会受到限制。
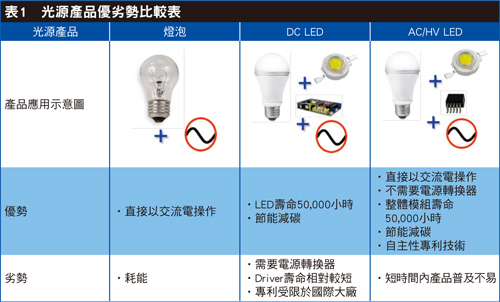
台湾自主性研发的高压(HV)LED技术产品,仅需简易的外加驱动电路,即可直接以市电110伏特(V)/220V驱动操作,并具备90%高功率因数(PF)、95%高能源利用率、高发光效率等优点。目前已于国际上取得发展先机,国内厂商晶元光电已陆续将HV LED晶粒产品出货给国外各家及应用大厂使用,国内也有多家相关厂商投入HV LED照明光源产品的开发,是为未来照明光源主流趋势。
迥异DC LED 驱动方式 HV LED特性和设计大相迳庭
高压LED是以半导体制程方式,将多颗微晶粒置于同一基板上,再加以串接而成,其所需之制程技术与传统LED十分近似。然而,由于驱动方式的不同,特别是在交流电驱动条件下,高压LED的特性和设计方向与传统LED有显著差异。
图1为高压LED晶片结构示意图。多颗制作于同一基板的微晶粒间以金属导线连结串接,而高压驱动电流则经由末端的两个打线垫片进入微晶粒串。由图2的微晶粒结构侧视图中,则可发现单颗微晶粒的结构与传统LED间主要的差异,仅在于尺寸的不同,其他包括透明导电层、表面粗糙化、图案化蓝宝石基板等可提升传统LED效率的技术,也同样适用于高压LED。
图1 高压LED结构上视图
图2 成长于蓝宝石基板的GaN微晶粒侧视结构图
‖
高压LED与传统LED晶片两者在制程上的主要差异点在于绝缘基板的使用、绝缘沟槽的蚀刻及金属导线的制作。高压LED的核心概念是将制作于同一基板的多颗微晶粒加以串接而成,因此使用绝缘基板确保微晶粒间的电性绝缘是高压LED得以正常操作的基本条件。对于以氮化镓(GaN)材料所成长的LED而言,由于所使用的蓝宝石基板具备极佳绝缘特性,因此只要将微晶粒间的沟槽蚀刻至基板裸露,即可达到良好的电性绝缘。
此外,由图3中可发现,虽然微晶粒间的绝缘沟槽是让高压LED得以正确运作的必要结构,但却也使得高压LED晶片整体的可发光面积缩减。虽然在概念上,越细窄的绝缘沟槽可增加高压LED晶片的可发光面积,但相对也会提升制程的困难度。
图3 高压LED晶片SEM照片
绝缘沟槽的侧壁须使用介电材料被覆保护,以避免金属导线通过表面时,P-N材料间发生短路情况。但当绝缘沟槽过于细窄时,无论使用化学气相沉积或蒸镀方式制作介电材料薄膜,均可能发生被覆不完全的情况,并导致微晶粒的P-N材料短路失效。同样地,过于细窄的绝缘沟槽也会使得金属蒸气不易进入,造成金属导线薄膜的厚度过薄或甚至不连续,进而导致高压LED晶片的串联电阻增加,或甚至有开路失效情况发生。
为提升介电材料与导线金属薄膜的制程良率,将绝缘沟槽制作成为开口向上的倒梯形结构是一可行方式。图4中所显示的倾斜侧壁结构除可提升微晶粒与高压LED的制程良率外,非矩形的几何结构对微晶粒的光取出效率提升亦有帮助。此外,为避免金属遮蔽降低高压LED发光效率,铺设于微晶粒间的金属导线必须同时具备低阻抗与低光线遮蔽之特性。制作细且厚的金属导线是达成上述目标的方法之一,而使用透明金属氧化物,如氧化铟锡(ITO)或氧化锌(ZnO)等,做为导线材料亦是可行手段,两者均有助提升高压LED发光效率。
图4 具倾斜侧壁、倒梯形开口的微晶粒结构
以下针对国内外的HV LED技术研发现况,做一概略性的整理。
突破微晶粒制程桎梏挑战 台湾取得HV LED发展先机
台湾自主性HV LED技术,系以高压直流或交流电等形式直接驱动LED,突破微晶粒制程技术,发展出具有高电压低电流操作优点的HV LED产品,大幅提升LED晶粒之发光效率,并在国际市场上取得了技术发展先机。此技术结合简易的驱动电路,即可有效提升能源转换和使用效率,并可应用于小型化设计的照明应用,大幅提升LED应用产品的可塑性。
‖
工研院已将相关微晶粒开发专利技转国内LED大厂晶元光电,使其拓展至HV LED领域,并成功开发出具备高发光效率的HV LED晶片,陆续与国际LED知名大厂及国内如亿光、葳天、福华、光宝等LED封装厂进行合作,推出HV LED相关应用照明产品(表2)。
目前国内HV LED晶粒系采用单晶片式的微晶粒结构组合设计,可量产的晶粒蓝光效率可达430mW/W;若制作成白光发光元件,则白光效率可达130lm/W。依据产品现况及未来开发规画,预计至2014年年底,HV LED晶粒效率可达600mW/W,白光效率将可达到180lm/W。
加紧投入研发 外商HV LED技术迭有进展
以下将介绍国外LED厂商发展HV LED的现况。
Philips
该公司第一代高压式LED Luxeon H50-1(50V)型号封装元件(图5),于85℃操作环境下,投入电力为1W,其发光通量可达67 lm。
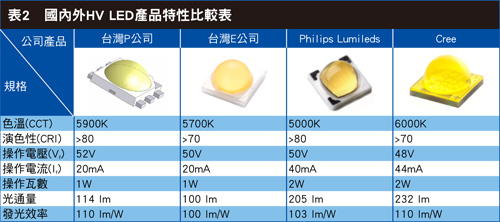
图5 Philips Lumileds所开发的HV LED元件
其后发表的Luxeon H(100V与200V)型号封装元件,于85℃操作环境下,投入电力为4W,其发光通量可达360lm。
2012年发表的新一代HV LED封装元件Luxeon H50-2,可操作于环境温度85℃,以50V电源为驱动条件,其操作瓦数为2W,光源色温5,000K,元件的光通量可达205lm,光源色温2,700K,元件的光通量可达165lm;操作于室温环境25℃,光强度约略可提升至1.1倍,相对于输入电压电流光强度呈直线增加。
上述产品透过简易的高压晶片组合,拟克服传统DC LED搭配驱动电路之体积过于庞大,且使得设计难度受限的问题,有效缩小灯具体积,且提升照明灯具之设计弹性,如常见的球泡灯、蜡烛灯及吊饰灯,俨然已朝向新一代LED照明元件之发展方向迈进。
美国科锐(Cree)于2011年推出高压驱动的HV LED封装元件XLamp XM-L及XT-E(图6),可操作于环境温度85℃,以46V电源为驱动条件,其操作瓦数分别为2W及1W,光源色温5,000K,元件的光通量分别可达240lm及114lm;光源色温2,700K,元件的光通量分别可达172lm及87lm;操作于室温环境25℃,光强度约略可提升至1.15倍,相对于输入电压电流,光强度呈直线增加。
图6 Cree所开发的HV LED元件
Cree之高压LED产品,提供一种封装尺寸更小之选择,搭配转换效率较高的高压驱动电路,有效的减少驱动所造成的损耗,HV LED可套用于空间受限之照明应用上,诸如B10、GU10和E17等小型灯泡产品,大幅提升产品的可应用范围及使用弹性。
首尔半导体
韩国首尔半导体(Seoul Semiconductor)推出的Acrich2光源模组(图7、8),依据使用者需求选择分为120V或220V两种操作型号,其操作瓦数为4.3W,光源色温5,000K,元件的光通量可达320lm;光源色温4,000K,元件的光通量可达310lm;光源色温2,700K,元件的光通量可达290lm。
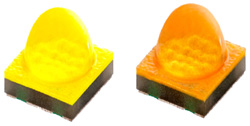
图7 首尔半导体所开发的HV 模组
图8 首尔半导体所开发的AC/HV LED光源模组电路等效示意图
‖
首尔半导体之高压交流LED产品,直接于封装上整合驱动IC元件,因此光源模组可直接操作在交流电压的环境下,不须外加电源转换器或驱动电路,可直接应用在照明产品上,提升下游厂商的使用便利性。其中的驱动IC,结合多段式切换控制的设计,可于较低电压操作区间即可启动部分的HV LED元件,因此提升整个光源模组的功率因数,这将有助于减少能源损耗,提升整体光源效率。 此外,由于将电路整合于驱动IC元件上,整体HV LED光源模组使用的外部元件大幅减少,光源模组的可靠度将能够提升,使得整体操作寿命更接近于LED操作寿命之理论值。
HV LED适用中功率光源
HV LED照明光源有几个竞争产品,分别是有机发光二极体()、被动式有机发光二极体(PLED)、DC LED和AC LED。
由于相关替代性产品如OLED及PLED,挟带着低直流电压、均匀面发光、发光效率可达80lm/W和60lm/W等优点,准备进攻显示器及背光源的市场,在技术及实用性可与现有的LED匹敌。但这类替代产品目前发光效率尚不及LED,因此整体而言,尚无较明显的威胁性产生。
DC LED以直流电流源驱动(图9),其元件具备体积小、发光效率高等诸多优点,可应用于显示、车用、指示、装饰及照明等广泛的应用领域,惟须外加交直流电源转换电路,使得市电高电压交流电可以降压,并转为低电压直流电来驱动DC LED,此外,电源转换电路亦往往造成能源的损耗。
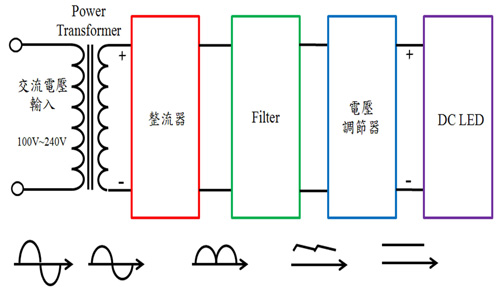
图9 DC LED的驱动电路概念示意图
在另一方面,DC LED使用寿命理论上可达30,000小时以上,但电源转换电路之寿命平均约5,000小时,因此在DC LED尚未失效前,照明灯具往往因为驱动电路先行损坏而造成失效。
另外,驱动电路的存在,也大幅增加整体光源模组的体积,因此较不适用于中低瓦数的光源产品,目前较适合DC LED技术的应用领域为高瓦数之光源应用产品,驱动电路体积相对于光源整体体积之比例则大幅下降。
为克服外加驱动电路所造成的能源损失、体积过于庞大等问题,AC LED产品遂应运而生,透过微晶粒的排列设计组合,使用数十颗微晶粒之串并连接,毋须外加安定器和AC-DC转换器,即可直接以市电110V/220V来驱动点亮(图10),大幅提升操作便利性,并有效缩减了光源体积,其产品功率因数可达85%以上,电源效率可达95%以上,是真正节能减碳的新技术。
图10 AC LED的驱动电路示意图及晶粒亮暗操作情况
‖
但是,由于AC LED是以串并接的设计方式来使用,在交流电的驱动环境进行时段性操作点亮,将使得晶片面积的有效利用率稍低,在同一时间部分微晶粒是停止操作的。由于AC LED无需太过繁杂之驱动元件,因此不需要额外之散热需求,适合应用在低功率的光源应用,如小夜灯、蜡烛灯等产品。
由AC LED技术所拓展的HV LED技术(图11),透过简易的微晶粒单向串接技术,外加一简易的桥式整流元件,即可直接操作在交流电压的环境下,除具备功率因数高(PF>90%)、电源效率高(>95%)及简易之驱动电路组合外,更具备LED高发光效率、长操作寿命等优点。
图11 HV LED的驱动电路概念示意图
虽然DC LED、AC LED、HV LED等技术产品之间具备相当的共通性,但也由于产品操作特性的不同,使得三种LED技术产品各自拥有其适合扮演的应用产品角色。其中HV LED较适合1W?20W之中功率光源应用,正是目前室内主流照明所在的操作范围内,确实有加紧脚步开发之必要,以加速HV LED于室内照明的普及。
欠缺标准方案 HV LED产业发展受阻
台湾自微晶粒LED技术发展开始,已长期累积HV LED元件相关之技术能量,结合大中华地区之应用市场,可利用先天优势来主导相关技术产品之推动。
国内厂商领先全球推出HV LED产品,建立真正属于台湾主导的自主化LED产品,并加速推动使其技术实际商品化,目前国内已有多家厂商积极投入相关产品研发与销售。但是各家厂商自定HV LED开发规格,须针对不同产品进行设计,造成资源浪费,提高样品库存量。
HV LED在实际应用产品上,没有共通之驱动电路设计,不同的应用需求或操作规格,须要各自开发相对应不同的驱动电路系统,提高所需开发成本。另外,由于操作瓦数及散热之需求,各家厂商也须分别开发不同的封装载具。
由上述可知,虽然台湾已具备HV LED产品的技术基础,但目前整个环境缺乏模组标准化之建立,无法提供一个可为国内厂商共通使用之标准化光源,造成资源的浪费及技术产品的发散。因此,HV LED产品虽具备光源特性上的优势及产品竞争力,但产品比重尚无法大幅提升,仍需要一段时间来整合及推动产业标准化。
供应链渐具雏形 台湾HV LED厂具高竞争力
台湾是全球最大的LED生产国,具备完整的产业链,在生产成本、供货稳定度等生产条件,具备极大优势与机会。特别在HV LED技术上已具备自主性,并已于国际上取得专利布局先机,有机会透过HV LED技术,于国际市场上创造一波潮流。
同时,在HV LED技术发展优势之前提下,订定并开发台湾HV LED技术标准化规格产品,降低生产所需成本,提升产品操作便利性,必然可使台湾于HV LED相关技术发展迅速大幅领先国外厂商,进一步奠定HV LED光源的市占,并提升技术产品应用优势。
LED之家小提示:若文章图片无法显示,又急需查看图片,请将需求文章的网址发往邮箱:wantled@163.com ,本站将尽快将相关图片回复到您的邮箱。
相关词语:
LED应用产品 LED技术 LED应用 LED照明 LED光源 首尔半导体 LED产品 LED封装 LED生产 国际LED LED特性 高功率白光 LED晶片 国内LED LED产业 LED领域 产业发展 OLED 晶元光电 驱动IC